Retention and recruitment in the frontline workforce is a challenge for US manufacturers, both large and small. Some firms are turning to automation to solve these problems, but initial research shows that deploying automation without also making job quality improvements may do more harm than good.
For manufacturers that are considering integrating automation, be it artificial intelligence (AI) or otherwise, into their operations, the recommendations presented here provide guidance. They are based on interviews with experts, research, and best practices from leading firms in the field on how to deploy automation in a way that raises job quality, improves retention and recruitment, and protects their bottom line.
The Challenges
1
Reduced human oversight in AI software and data-driven automation brings a new set of risks.
2
New and changing technologies require new skillsets, but manufacturers are struggling to source suitable talent.
3
Automation deployment in manufacturing can lead to deskilling and higher churn, intensifying retention challenges for the industry and contributing to institutional brain drain.
Busy Executive on the go?
Download printable PDFs of the Recommendation Spotlights and Frontline AI Cheat Sheet.
Business Motivations
Manufacturers are turning to AI tools to increase the productivity of plants (reducing downtime, reducing waste, increasing capacity per line) while reducing the amount of human capital (both number of workers and hours worked) required to perform certain tasks. The tax structure in the US incentivizes automation, since taxes are higher for labor and lower for capital.
Severe production disruptions driven in part by the COVID-19 pandemic have created a very strong incentive to automate work. A study by Oxford Economics estimates that 20 million manufacturing jobs will be automated by 2030. Given the industry’s challenging history with employee retention and recruiting, some companies are looking at automation as a silver bullet for all of their workforce challenges.
Applications of Automation
The Center for Economic Studies found that as many as 64% of US workers and 72% of manufacturing workers are exposed to automation technologies like AI, robotics, and specialized software, based on data from the US Census Bureau’s 2019 Annual Business Survey. Adoption is concentrated in large firms. Common applications of these technologies include:
- Maintenance: Predictive maintenance software leverages a network of sensors on machinery to detect signs of wear so that servicing can be planned pre-emptively instead of in response to expensive breakdowns.
- Quality control: Companies are automating processes, often through a combination of sensor data and AI software, to identify when a product fails a quality control check.
- Dirty, dull, and dangerous work: Machines are used to perform repetitive, specific manipulation tasks, such as processing components on an assembly line, and can be deployed in environments where temperatures or aerosols are unsafe for humans.
- Streamlining human-computer interactions: To speed up redundant computer interactions such as copy-pasting information across platforms, companies use digital rule-based programs called “robotic process automation” that replicate the interactions of a human navigating through computer interfaces.
- Shift scheduling: AI-driven tools are used for “smart scheduling” which can reduce unassigned time. Although these systems can be designed and used to give workers more control over their hours, they are frequently used as a form of worker surveillance, cited as a cause of high worker burnout and turnover.
Impacts of Automation
Availability of Jobs
Research on the impact of AI adoption on the availability of jobs and wages is not clear-cut. Some groups predict that the impact will depend on the specific use case and application of the AI tool, while others say that there is a real chance that AI deployment will ultimately lead to pervasive unemployment. Regardless of the net impact of AI adoption on jobs overall, it is clear that some jobs will be lost, leading to:
- Fewer jobs focused on routine tasks: Workers without specialized skill sets and workers performing routine or replaceable tasks may struggle to compete with automation.
- Disproportionate displacement: Women (nearly 30% of the frontline manufacturing workforce), workers of color (nearly 30%), and workers without a 4-year degree (nearly 71%) are more likely to face disproportionate displacement.
- Lower barriers to entry: Automation that simplifies tasks can make a role accessible to a larger number of potential workers, but this can also result in greater competition for roles.
- Training challenges: The benefits of AI tools are greater for those with specific training and roles, disproportionately putting certain workers, especially those over 40, at higher risk of job displacement due to automation.
Job Quality
People promoting AI as beneficial to the future of work have advocated that it can free up workers from dirty, dull, or dangerous tasks, allowing them to instead focus on higher-value activities that enable upward mobility internally within the organization. Commonly mentioned benefits include:
- Making industrial work safer: Minimizing direct contact between a human worker and dangerous machinery via robotics can improve safety in industrial workplaces.
- Reducing physical labor requirements: Manufacturing work has historically been physically demanding and taxing, limiting the number and tenure of workers in the field.
- Freeing workers up from undesirable labor: Automation can reduce the amount of necessary tedious or repetitive work.
However, 2022 research from the Partnership on AI has indicated that, in fact, the opposite is happening:
“Current implementations of AI in work are reducing workers’ opportunities for autonomy, judgment, empathy, and creativity…Workers in US warehouses with higher degrees of AI implementation often had less variety in their tasks and more technological guardrails to assist them in performing them correctly.”
According to these findings, which analyzed interviews with frontline workers in manufacturing, call centers, and data annotators who work with AI tools, the main threat of AI deployment lies not in reducing the number of available jobs for workers, but in decreasing the quality of work, by:
- Placing harmful pressure on workers: Algorithmic management tools are often used to push intense, algorithmically-set productivity quotas.
- Reducing skill requirements to do certain work: Employers risk “deskilling” workers, where workers learn less about the processes they are contributing to, disrupting pathways to higher-paying work and reducing institutional wisdom.
- Minimizing worker voice and agency: Using tools to reduce worker autonomy leads to higher rates of attrition.
Maximizing the Benefits and Minimizing the Harms
Managerial decisions play a substantial role in shaping the impact of technology. Employers have an opportunity to lead and reap the benefits of implementing worker-centered processes when introducing these new tools. By doing so, companies not only foster a positive work environment but also enhance their competitive edge, ensuring sustainable growth and minimizing potential pitfalls associated with technology adoption.
Aspen Digital, in consultation with experts from academia, civil society, and industry, has developed the following recommendations on how to integrate automation into the manufacturing frontline responsibly. At a high level, getting the most out of automation requires thinking of workers as investments and assets that must be leveraged. The following themes represent best practices that are further detailed in the recommendations below:
- Upskilling: Train the workforce to adapt to new skills automated tools require.
- Human-in-the-loop: Maintain human review and control of automated or AI-informed decisions.
- Participatory design: Use tools that incorporate feedback from and address pain points of the workers themselves—people who will actually be using the tools.
- Human interaction: Emphasize and support human-to-human interaction at work.
- Supportive, not prescriptive, tools: Use tools that are meant to increase the agency of workers.
- Transparency: Be transparent with workers about the benefits and risks of automated tools, both to the firm and to them.
- Predictability: Look for and evaluate tools in part based on whether they bring predictability into the frontline workplace (such as a scheduling tool that makes it easier for workers to plan their shifts).
- HR foundations: Attract and retain talent with competitive compensation and benefit packages.
The following recommendations may be more ambitious for smaller firms, so buy-in from leadership will be pivotal. Small firms should consider:
- Collaborating on best practices with other firms in their region through industry-sector partnerships.
- Partnering with local community colleges for training and upskilling.
- Creating a registered apprenticeship program with resources from the Department of Labor.
- Using regional Manufacturing Extension Partnership (MEP) resources.
- Tapping into their local workforce development boards.
- Consulting organizations like the Workforce & Organizational Research Center (WORC), America Works, the Urban Manufacturing Alliance, and the Institute for the Future of Work.
Case Study
The Northland Workforce Training Center in Buffalo, NY offers for-credit, certificate,, and degree programs through partnerships with State University of New York colleges, Alfred State and Erie Community College, integrating practical experiences like co-ops, apprenticeships, and internships in advanced manufacturing. Read more about the impact.
The recommendations below are tailored to meet three goals shared by leaders in manufacturing:
- Reduce the risks of automated systems.
- Upskill to get the most out of automation investments.
- Retain workers and their valuable institutional knowledge.
To read about these goals and the recommendations to address them in more detail, please see the accompanying Goal Spotlights for each goal. The Frontline AI Cheat Sheet also contains helpful terminology and more details on strategies for worker engagement.
Issues for further exploration
- Large and small manufacturers do not equally enjoy the benefits of AI and automation. Smaller manufacturers are often limited in their ability and resources to initiate conversations on workforce development. Early and clear leadership from larger manufacturers in partnership with their vendors and suppliers can help steer the industry goals in a direction that prioritizes worker well-being.
- Transitioning to automated manufacturing while prioritizing job quality is a challenge. Industry-wide foundational and fundamental cultural shifts are required where the frontline workforce is viewed as an investment and asset that must be leveraged.
- Manufacturing employers and labor representatives are frequently portrayed as opposed, but they share many goals when it comes to the impacts of technology regarding staff retention, productivity, and resilience. Successful implementation of these recommendations requires collective action and continued engagement with key allies such as labor groups, employer coalitions, technology vendors and civil society.
Actionable Recommendations
To read about these goals and the recommendations to address them in more detail, please see the accompanying Goal Spotlight for each goal. The Frontline AI Cheat Sheet also contains helpful terminology and more details on strategies for worker engagement.
Goal 1: Reduce the risks of automated systems
At A Glance
- Reinforce to managers that AI tools can (and do) make mistakes.
- Maintain managerial decision-making and human oversight of automated systems.
- Develop clear internal guidelines for identifying contexts in which AI should not be used, such as in hiring.
- Evaluate the impacts of deploying automated systems on your workforce by identifying and tracking KPIs that measure employee satisfaction, health, and skill development, such as internal promotion rate, injury rate reduction, and employee satisfaction index.
- Ensure that an AI tool was designed to meet your specific needs by consulting workers.
- Set up real-time feedback loops during and after deployment using insights from the frontline. For more resources, see Strategies for Worker Engagement.
- Use a combination of quantitative KPIs and qualitative worker feedback via surveys or managerial check-ins to evaluate physical and mental health impacts of deployed automated systems.
- Prioritize informed consent prior to data collection.
- Ask technology developers or vendors specific questions about their products including about your right to repair, the interoperability of their tools, and the ownership of data collected.
Goal 2: Upskill to get the most out of automation investments
At a Glance
- Identify skill gaps and provide training in basic digital skills based on what types of upskilling workers want.
- Use community college partnerships to develop high-value interpersonal skills such as knowledge-sharing, conflict resolution, and negotiation.
- Make upskilling accessible by making sure training opportunities are available on site, during work hours, in multiple languages, and with appropriate compensation for time spent.
- Provide training for a variety of skills and in a range of formats based on what workers prefer, such as cross-training workers on different technologies and mentoring programs and apprenticeships.
- Clearly outline economic and career mobility benefits for workers who participate in an upskilling program.
- Designate a worker or small group of workers as subject matter experts for new technology or specific functions of the new technology.
Goal 3: Retain workers and their valuable institutional knowledge
At a Glance
- Be straightforward and communicate clearly with workers about expected changes by providing comprehensible explanations of the AI system’s function, talking plainly about staffing changes, and avoiding technology or business jargon.
- Provide adequate (at least 8 weeks) notice to workers and unions before deploying new technologies.
- Get feedback and collaboratively define productivity goals, both anonymously and through high-touch options like workshops, when adopting new technology.
- Seek worker input when creating policies for algorithmic management and worker surveillance (e.g., wearable technology, sensors, and other monitoring systems), both of which can decrease job quality and impact retention.
- Provide a clear career growth plan and allow workers to advance professionally by providing advancement training and opportunities on a yearly or more frequent cycle.
- Deploy automation in ways that provide equal opportunities to employees of all backgrounds, regardless of race, age, gender, education, experience, native language, or other individual traits.
- Recognize and compensate workers for their role in training peers and new hires through initiatives such as microcredentials, scholarships, or paid management trainings.
- Deploy technology that will complement or support your workers’ professional identities. Complementary technologies are much more easily accepted and adopted.
Cheat Sheet: Feedback & common terms
At a Glance
High-touch Options
- Town Halls
- Small team meetings with an immediate supervisor or plant leadership
- Hands-on feedback sessions with a vendor
- Soliciting feedback through organized labor representatives, when applicable
This process can be especially
helpful for getting feedback at scale.
Low-touch Options
- Physical suggestion box or flip board
- Digital surveys or feedback forms
Make sure to respond to feedback in some form, otherwise low-touch options may not produce constructive criticism!
Technology Terms
- Artificial Intelligence
- Automation
- Data
- Computer Vision
- Robotics
- Algorithmic Managment
Job Quality Terms
- Frontline
- Upskilling
- Reskilling
- Deskilling
Acknowledgements
This work was made possible with the support of PepsiCo, Inc. We’re grateful to Dr. Athina Kanioura and her team who supported our research.
Thanks also to Eleanor Tursman, Morgan McMurray, Elizabeth Miller, Anahita Sahu, Devon Regal, Haley Glover, B Cavello, and our other Aspen Institute colleagues for their contributions to this work.
Share your Thoughts
If this work is helpful to you, please let us know! We actively solicit feedback on our work so that we can make it more useful to people like you.
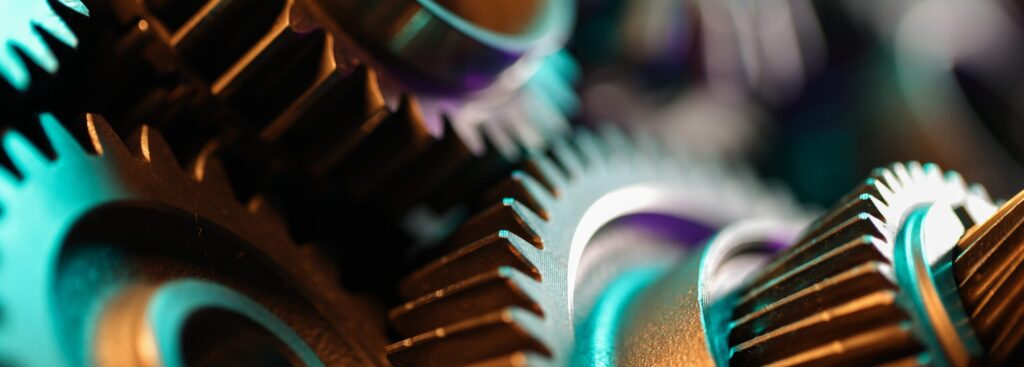